Application of Nano Ceramic Balls in Gold Mining: Comprehensive Analysis and In-depth Discussion
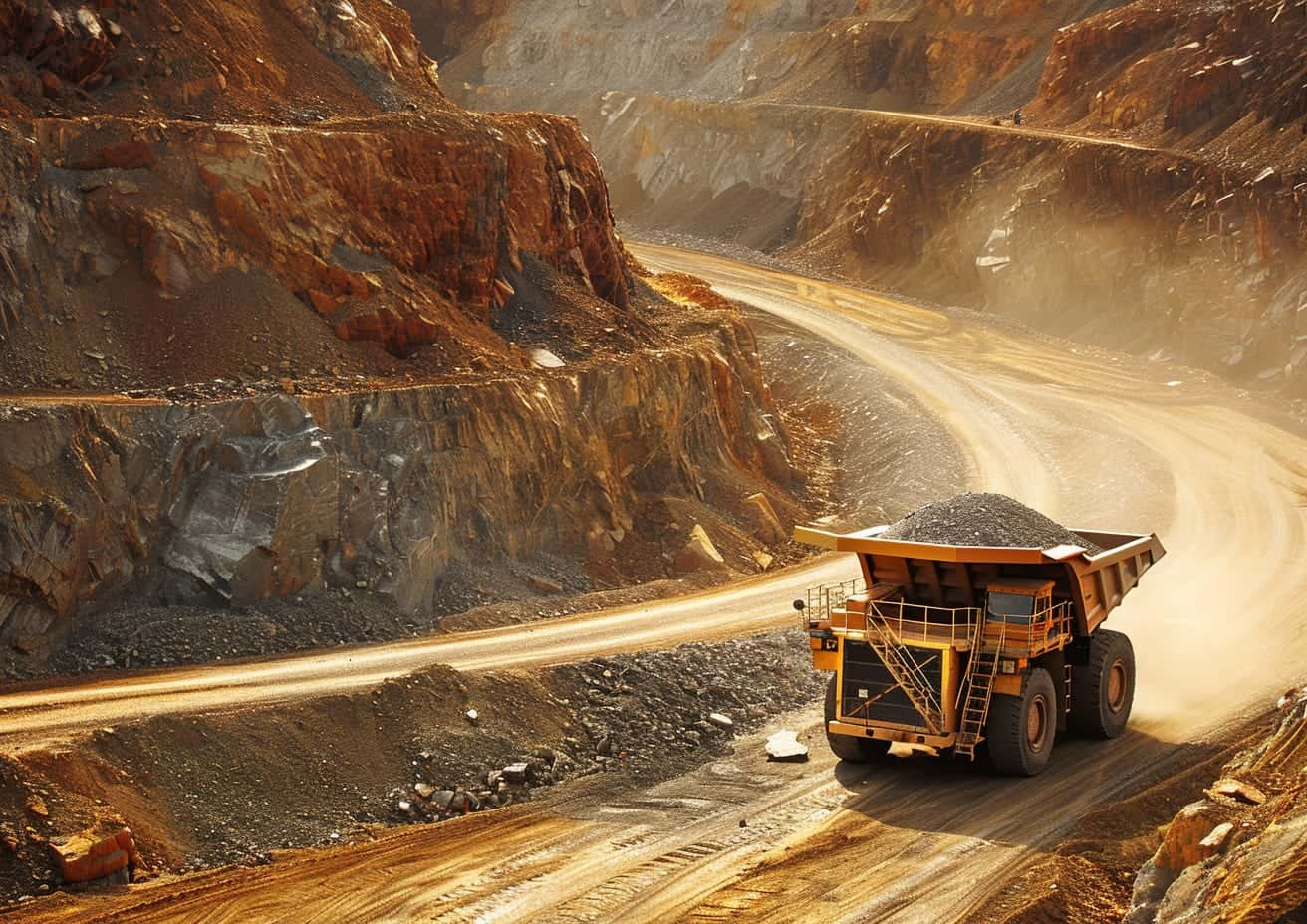
I. Introduction
The gold mining industry is constantly seeking advancements in technology to improve efficiency, reduce environmental impact, and lower costs. A key area of focus has been the development of more effective grinding media. Nano ceramic balls, as an emerging material, have begun to make their mark in gold mining due to their unique performance characteristics. These balls offer numerous benefits and present new opportunities for improving the gold mining process. However, like any material, they also have their own set of advantages and limitations. This article aims to provide an in-depth analysis of the application of nano ceramic balls in gold mining, including their advantages, disadvantages, key selection criteria, and specific application scenarios. The goal is to offer comprehensive and in-depth reference material for professionals in the gold mining industry to promote the rational application and technological innovation of nano ceramic balls in this field.
II. Advantages of Nano Ceramic Balls in Gold Mining
Nano ceramic balls exhibit a Mohs hardness of around 9, outperforming traditional steel balls in wear resistance. In months-long gold ore grinding, their minimal wear lessens media replacement frequency. This cuts costs and boosts production efficiency, as seen when their wear is a fraction of steel balls' in continuous operations.
These balls are inert, with grinding debris not dissolving in sodium cyanide. In gold mining's cyanide leaching, traditional high-chromium steel balls release iron impurities that react with cyanide. This hikes reagent costs, reduces gold leaching efficiency and recovery. Nano ceramic balls prevent this. Their stable chemistry ensures efficient, stable leaching, cuts pollution, aids compliance, and improves economic and environmental gains.
With a density of about 3.7 g/cm³ and high hardness, nano ceramic balls apply optimal force on ore. In coarse grinding, they break large ores; in fine grinding, their uniform size distribution precisely controls particle size. This boosts -400 mesh (approx. 38 μm) particle proportion, crucial for gold recovery. It elevates production efficiency, product quality, and enterprise competitiveness.
Nano ceramic balls' great wear resistance curbs wear on ball and stirred mills' key parts like spiral liners. This slows component wear, extends equipment life. Less maintenance, downtime, and better operation efficiency follow, underpinning stable production and enterprise growth.
Gold mining often has hot processes. Nano ceramic balls endure high temps without performance shifts. Stable in normal or high heat, they ensure consistent grinding. This offers process flexibility, helping handle complex production setups and requirements.
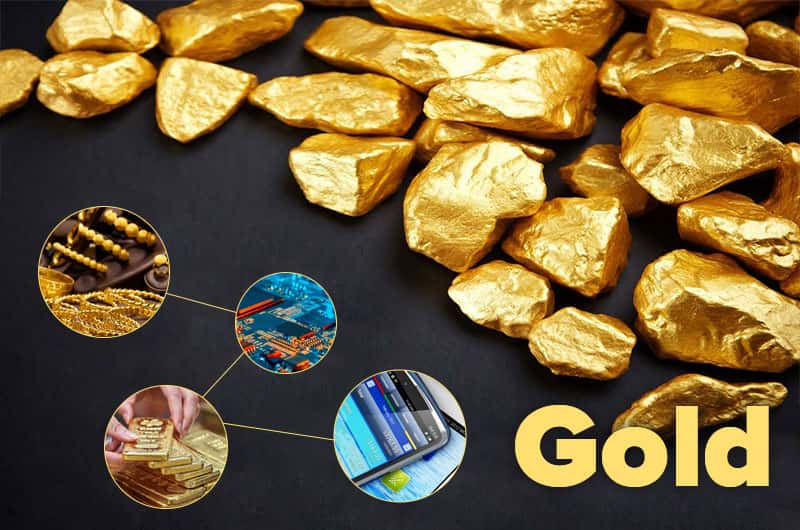
III. Disadvantages of Nano Ceramic Balls in Gold Mining
(I) Relatively High Brittleness
The inherent characteristics of ceramic materials determine that nano ceramic balls have a certain brittleness. During the grinding process of gold mining, if nano ceramic balls are subjected to relatively large impact forces or are in working conditions with stress concentration, they may break. Once broken, it will not only affect the normal use of nano ceramic balls themselves and lead to a decline in their grinding performance but also the fragments generated by the breakage may be mixed into the ore products, causing adverse effects on product quality, such as affecting the subsequent cyanide leaching effect. However, through reasonable engineering design and scientific usage methods, this risk can be reduced to a certain extent. For example, optimizing grinding process parameters, precisely adjusting grinding time, rotation speed, feeding speed, etc. according to ore characteristics and equipment conditions; strictly controlling the particle size and shape of the fed ore to avoid overly large or irregular particles from causing instant excessive impact on nano ceramic balls; adopting appropriate ball adding systems and equipment internal structure designs to reduce the generation of stress concentration points.
(II) Relatively High Cost
The preparation process of nano ceramic balls is relatively complex and requires advanced technology and equipment, which leads to relatively high production costs. Compared with traditional grinding media such as steel balls, the initial purchase price of nano ceramic balls is often much higher. For some small gold mining enterprises with limited budgets, this may limit their large-scale application to a certain extent. However, from the perspective of long-term operation costs and comprehensive benefits, due to the good wear resistance, long service life, ability to reduce equipment wear and improve production efficiency of nano ceramic balls, in some cases, their overall costs may not be higher than those of traditional grinding media, especially for large-scale, long-term and stable gold mining projects.
(III) Strict Requirements for Filling Rate
In the commonly used grinding equipment in gold mining such as vertical mills, the filling rate of nano ceramic balls has a crucial impact on the grinding efficiency and needs to be precisely controlled. When the filling rate is too high, the collisions and frictions between nano ceramic balls are too frequent, which will lead to an increase in energy consumption. At the same time, it may cause the material flow inside the mill to be unsmooth, affecting the grinding effect and reducing production efficiency; when the filling rate is too low, the grinding function of nano ceramic balls cannot be fully exerted, resulting in insufficient grinding and failure to meet the product particle size requirements. Therefore, determining the appropriate filling rate needs to comprehensively consider various factors such as mill type, ore characteristics, and grinding process requirements, which undoubtedly increases the operational difficulty and management complexity in the production process. Enterprises need to be equipped with professional technicians and complete monitoring equipment to monitor and adjust the filling rate of nano ceramic balls in real time to ensure that the grinding process is always in the best state.
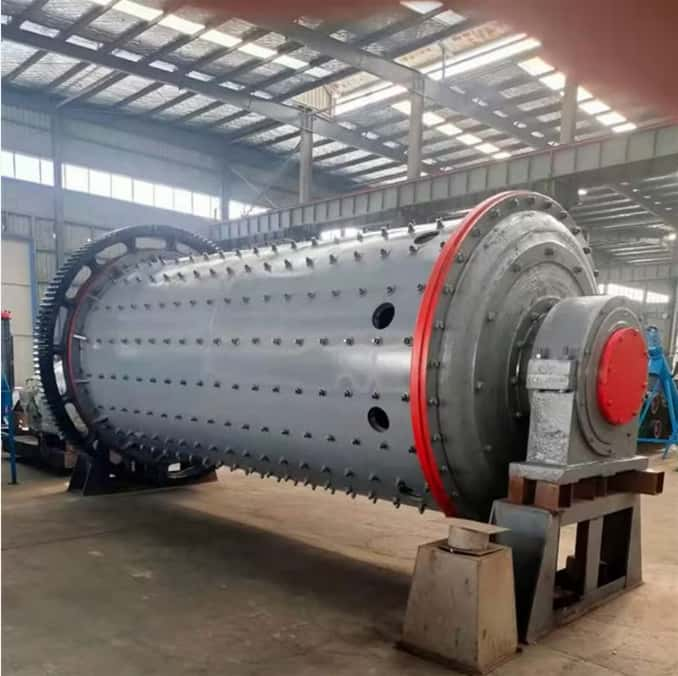
IV. Key Points for Selecting Specifications and Models of Nano Ceramic Balls
(I) Parameters of Grinding Equipment
Mill Type and Size
Different types of mills, such as vertical spiral stirred mills and ball mills, have differences in their internal structures and working principles, which directly determine different requirements for the specifications and filling rates of nano ceramic balls. For vertical mills, the internal spiral structure and stirring method have a unique impact on the motion trajectory and energy transfer of nano ceramic balls. Generally speaking, due to the relatively small internal space of small vertical mills, smaller-sized nano ceramic balls need to be selected to ensure that they can move fully in the limited space and achieve good grinding effects. While large vertical mills have a larger internal volume and can accommodate larger-sized ceramic balls, and the filling amount also needs to be adjusted accordingly to match the power and production capacity requirements of the mill. Ball mills also have different adaptabilities to the size and filling rate of nano ceramic balls according to factors such as the diameter, length of the cylinder, and the structure of the liner. For example, ball mills with a smaller cylinder diameter may be more suitable for using smaller-sized nano ceramic balls to ensure that the balls can form an effective grinding layer inside the mill.
Mill Power and Rotation Speed
The power and rotation speed of the mill are important factors affecting the motion state and energy transfer efficiency of nano ceramic balls. Mills with high power and high rotation speed can provide greater kinetic energy for nano ceramic balls, making them have stronger impact force. In this case, it is more appropriate to select larger-sized or heavier ceramic balls so as to better handle gold ores with higher hardness. For example, for some quartz vein type gold ores with relatively high hardness, using nano ceramic balls with a diameter of 20 - 25 mm in mills with high power and high rotation speed can effectively break the ores. On the contrary, if the mill power is
relatively low and cannot provide sufficient power for large-sized ceramic balls, it is more advisable to choose smaller and lighter nano ceramic balls. In this way, through multiple effective collisions of ceramic balls, the grinding of ores can be realized under low power conditions, ensuring the smooth progress of the grinding process and avoiding equipment overload problems caused by insufficient power.
(II) Ore Characteristics
Hardness of Gold Ore
The hardness of gold ore is one of the core factors in selecting the specifications and models of nano ceramic balls. For gold ores with relatively high hardness, such as quartz vein type gold ores (the Mohs hardness is usually between 7 and 9), it is necessary to choose nano ceramic balls with higher hardness and better wear resistance, and larger-sized ceramic balls should be given priority. This is because larger-sized ceramic balls can generate greater impact force during the grinding process, which is sufficient to overcome the resistance of high-hardness ores and break them. For example, nano ceramic balls with a diameter of 20 - 25 mm can be selected for coarse grinding operations. For gold ores with relatively low hardness, such as altered rock type gold ores, smaller-sized ceramic balls may be able to meet the grinding requirements. Although smaller-sized ceramic balls have relatively small impact forces, they can achieve effective grinding of low-hardness ores by increasing the number of collisions under the condition of a large quantity, and at the same time can better control the particle size distribution of products, avoiding energy waste and subsequent processing difficulties caused by excessive crushing.
(III) Requirements of Grinding Process
Product Particle Size Requirements
The particle size requirement of the final product in the gold mining process is one of the key indicators for determining the selection of nano ceramic balls. If the product particle size requirement is relatively fine, for example, if it is required that the proportion of particles below -400 mesh (about 38 μm) in the product is relatively high, then smaller-sized nano ceramic balls need to be adopted, and the grinding process needs to be optimized by finely adjusting parameters such as the ball adding system, grinding concentration, and filling rate. Smaller-sized nano ceramic balls can grind ore particles more precisely during the grinding process, gradually refining the particles to the required particle size range. At the same time, a reasonable ball adding system can ensure that different-sized ceramic balls form a good gradation inside the mill, improving the grinding efficiency; an appropriate grinding concentration can ensure sufficient contact and interaction between ceramic balls and ore particles; and an accurate filling rate can enable ceramic balls to play the best energy transfer and grinding effect in the mill. On the contrary, if the product particle size requirement is relatively coarse, under the premise of ensuring the effective dissociation of gold minerals, larger-sized ceramic balls can be selected, which can utilize their greater impact force to improve the grinding efficiency, reduce the grinding time and energy consumption.
V. Application Scenarios of Nano Ceramic Balls in Gold Mining
The application of nano ceramic balls in gold mining can be categorized into several key stages, each with specific roles and benefits. Understanding these scenarios helps in optimizing their use for enhanced efficiency and effectiveness in gold recovery processes.
(I) Ore Grinding Stage
Coarse Grinding Application
In the initial stage of gold mining, after the ore is extracted from the mine, the first process it faces is coarse grinding. Nano ceramic balls play an essential role in this process, effectively breaking larger pieces of gold ore into smaller particles. For instance, after the ore has been initially crushed by a jaw crusher or a cone crusher, it enters a ball mill for coarse grinding. The nano ceramic balls, with their high hardness (Mohs hardness of 9) and appropriate density (about 3.7 g/cm³), can exert significant impact force on the ore. Larger-sized ceramic balls (such as those with a diameter of φ25 - 30 mm) generate sufficient energy to quickly reduce the ore particle size from several centimeters or even more than ten centimeters to a few millimeters. This intense collision and friction between the nano ceramic balls and the ore particles gradually destroy the structure of the ore, providing suitable raw materials for subsequent fine grinding operations. Furthermore, due to the excellent wear resistance of nano ceramic balls, their wear during the coarse grinding process is relatively small, allowing them to maintain effective grinding performance for extended periods. This reduces the decline in grinding efficiency caused by media wear and minimizes downtime for equipment maintenance and media replacement, ultimately improving production efficiency and stability.
Fine Grinding Application
Following the coarse grinding stage, the fine grinding stage is crucial for refining the ore particles to meet the specifications required for subsequent processes, such as gold leaching. In this stage, nano ceramic balls continue to play a vital role. After the coarsely ground ore enters a stirred mill for fine grinding, smaller-sized nano ceramic balls (such as those with a diameter of φ10 - 20 mm) can be added. These smaller ceramic balls can grind the coarsely ground ore particles more precisely, as they can enter the smaller gaps between the ore particles, gradually refining them. By adjusting the ratio of different-sized ceramic balls, an effective grinding medium gradation system can be established. For example, during the fine grinding process, a ratio of large-sized to small-sized ceramic balls (e.g., 3:7) can be maintained, where the larger balls primarily handle crushing and energy transfer, while the smaller balls focus on fine grinding. This approach increases the proportion of particles below -400 mesh (about 38 μm) in the product, which is critical for improving gold recovery rates.
(II) Gold Leaching Stage
The gold leaching stage is another critical phase where nano ceramic balls can have a positive impact. As previously mentioned, their excellent chemical stability means they are inert media that do not dissolve any harmful substances during the grinding process. When the ground ore undergoes the gold leaching operation, the clean grinding environment provided by the nano ceramic balls ensures the purity of the chemical reagents used in the leaching process, such as cyanide. This purity reduces the interference of impurities on the reaction between gold and the leaching reagents, facilitating a smoother gold leaching reaction and improving overall efficiency. Additionally, compared to traditional grinding media, nano ceramic balls do not introduce new impurities that could affect subsequent gold extraction and purification processes, contributing to the overall quality of the final gold product.
(III) Tailings Treatment Stage
In the tailings treatment stage of gold mining, nano ceramic balls also demonstrate significant application value. Many tailings still contain valuable minerals that have not been fully recovered. By using nano ceramic balls for re-grinding the tailings, it is possible to further break down the tailings particles, enhancing the likelihood of dissociating and recovering valuable minerals. The good wear resistance and chemical stability of nano ceramic balls ensure that they maintain stable performance during the repeated grinding and treatment of tailings, reducing the consumption of grinding media and minimizing environmental impact. Moreover, through proper parameter adjustment and process optimization, the recovery rate of valuable minerals in tailings can be effectively improved, maximizing resource utilization in gold mining and reducing waste.
VIII. Conclusion
In conclusion, nano ceramic balls represent a significant advancement in the field of gold mining, offering numerous advantages such as high hardness, chemical stability, and optimized grinding effects. While there are challenges associated with their implementation, the potential benefits in terms of efficiency, cost savings, and environmental impact make them a valuable addition to gold mining operations. By carefully considering the selection criteria, application scenarios, and ongoing innovations, mining professionals can leverage the unique properties of nano ceramic balls to enhance their processes and contribute to the sustainable development of the gold mining industry. As the industry continues to evolve, the rational application and technological innovation of nano ceramic balls will play a crucial role in shaping the future of gold mining.