In the dynamic and highly competitive realm of the mining industry, the pursuit of optimal mineral extraction and processing techniques has become a top priority. Ceramic grinding balls have emerged as a game-changing innovation, particularly in lead-zinc mines where the stakes are high in terms of achieving high recovery rates and fine particle distribution. These advanced grinding media offer a host of benefits that set them apart from traditional counterparts and are poised to redefine the standards of efficiency and sustainability in the mining sector.
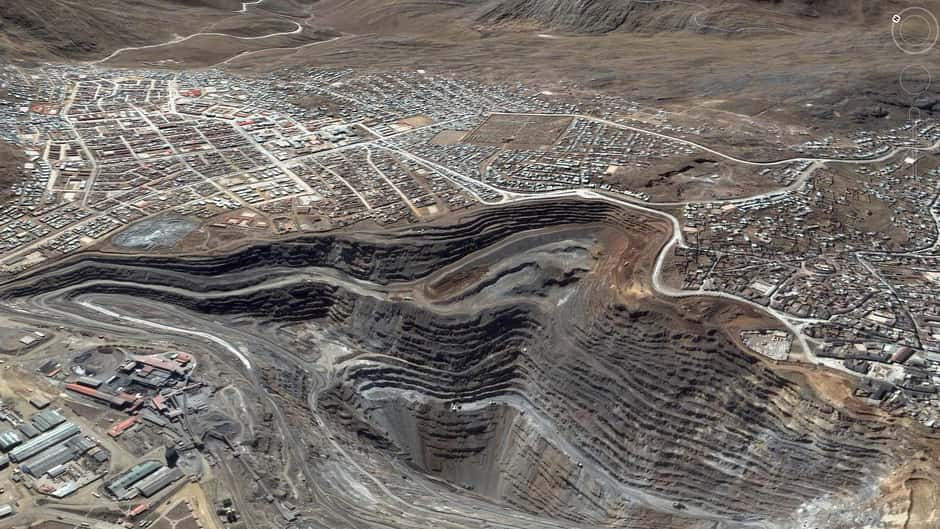
Understanding Ceramic Grinding Balls
Ceramic grinding balls are meticulously engineered using state-of-the-art materials such as zirconia, alumina, and silicon carbide. These materials possess a unique combination of properties that make them highly suitable for the rigors of fine and ultra-fine grinding applications. Zirconia, renowned for its high density and remarkable strength, imparts excellent grinding capabilities, especially in the realm of ultra-fine grinding where precision and durability are of utmost importance. Alumina, on the other hand, offers a cost-effective solution for medium-fine grinding operations without compromising on performance. Silicon carbide further contributes to the overall hardness and wear resistance of the ceramic balls.
One of the most significant advantages of ceramic grinding balls is their high density. This property allows them to exert greater force during the grinding process, ensuring efficient breakdown of the ore. Their exceptional wear resistance is a key factor in their success. Unlike traditional steel grinding media that tend to wear out relatively quickly, ceramic balls can withstand the abrasive forces for extended periods. This not only reduces the frequency of replacement but also minimizes the downtime of grinding equipment, which is crucial in a continuous mining operation.
Chemical inertness is another hallmark of ceramic grinding balls. In lead-zinc mines, where the composition of the ore and the quality of the concentrates are of prime concern, the prevention of unwanted chemical reactions is vital. Ceramic balls do not react with the ore, thereby ensuring the purity of the final product. Additionally, their low abrasion rates are a boon. This means that they lose very little material during the grinding process, maintaining a consistent size and shape. This consistency in turn leads to a more stable grinding performance over time. The uniform size distribution of ceramic grinding balls is yet another advantage. It enables precise control over the particle size reduction, which is a critical factor in downstream processes such as flotation.
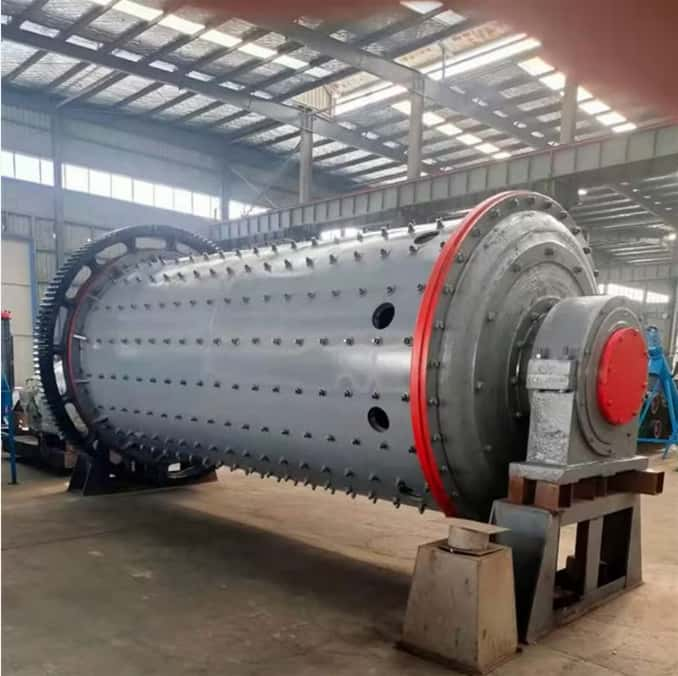
Key Benefits of Ceramic Grinding Balls in Lead-Zinc Mines
1. Enhanced Wear Resistance
The durability and wear resistance of ceramic grinding balls are truly remarkable. In lead-zinc mines, where grinding operations run continuously, the need for reliable and long-lasting grinding media is non-negotiable. The ability of ceramic balls to endure the harsh grinding conditions significantly reduces the frequency of replacement. This directly translates into lower operational costs. Fewer replacements mean less expenditure on new grinding media and also less labor and downtime associated with the replacement process. The increased uptime of the grinding equipment leads to higher overall productivity and profitability.
2. Minimal Contamination
Steel grinding media have long been a source of concern in lead-zinc processing due to the introduction of metallic impurities into the ore. These impurities can have a detrimental effect on the quality of the concentrates and can cause issues in subsequent processing steps such as smelting. Ceramic grinding balls, being chemically inert, eliminate this problem entirely. They ensure that the purity of the lead and zinc concentrates is maintained at the highest level, meeting the stringent quality requirements of the market and facilitating better downstream processing.
3. Energy Efficiency
The high density and consistent performance of ceramic grinding balls contribute to significant energy savings. In the energy-intensive mining industry, any reduction in energy consumption is a major advantage. Compared to traditional grinding media, ceramic balls require less energy to achieve the same level of grinding. This is because their density allows them to transfer more energy to the ore during each impact, resulting in more efficient grinding. The lower energy consumption not only reduces the operating costs but also has a positive environmental impact by decreasing the carbon footprint of the mining operation.
4. Uniform Particle Size Distribution
A more uniform particle size distribution is a crucial aspect of lead-zinc mining. In the flotation process, where minerals are separated based on their surface properties, a consistent particle size is essential. Ceramic grinding balls excel in this regard. They ensure that the particles are ground to a more uniform size, which in turn enhances the recovery rates of valuable minerals such as galena (PbS) and sphalerite (ZnS). The increased surface area of the uniformly sized particles also improves the interaction with flotation reagents, leading to better separation and higher overall recovery rates.
5. Environmental Benefits
Ceramic grinding balls are a step forward in sustainable mining practices. Their long lifespan means that less waste is generated in the form of worn-out grinding media. Additionally, their low abrasion rates result in a reduction in the generation of fine particulates. These fine particulates can have a negative impact on the environment, causing air and water pollution. By minimizing their production, ceramic balls contribute to a cleaner and more sustainable mining operation.
Applications in Lead-Zinc Mining Processes
1. Crushing and Grinding
The initial step in lead-zinc mining is the crushing of the ore to liberate the valuable minerals. Ceramic grinding balls play a crucial role in this process, especially in ball mills and regrind mills. They are used to grind the crushed ore to the desired particle size for optimal liberation. The efficient grinding achieved by ceramic balls sets the stage for the subsequent flotation and separation processes. By ensuring that the minerals are properly liberated, the recovery rates of lead and zinc can be maximized.
2. Flotation Process Enhancement
Flotation is a cornerstone of lead-zinc mining, where the separation of minerals based on their surface properties takes place. Fine grinding using ceramic balls is a key enabler of this process. The finer the grinding, the larger the surface area of the particles, which in turn improves the interaction with flotation reagents. This leads to better separation of lead and zinc minerals from the gangue, resulting in higher recovery rates and purer concentrates. The uniform particle size achieved by ceramic grinding balls further enhances the efficiency of the flotation process, ensuring that the valuable minerals are effectively separated and recovered.
3. Tailings Management
Effective grinding with ceramic balls has a significant impact on tailings management. The reduced size of the tailings due to efficient grinding makes them easier to handle and dispose of. This is essential for compliance with environmental regulations and for sustainable mining practices. Smaller tailings can be more easily stored or processed further, reducing the environmental footprint of the mining operation.
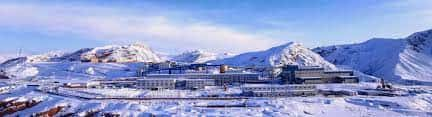
Case Studies in Lead-Zinc Mines
Case Study 1: Efficiency Improvement in an Asian Lead-Zinc Mine
A lead-zinc mine in Asia made a strategic decision to replace steel grinding balls with ceramic grinding balls. The results were nothing short of impressive. The grinding efficiency increased by 15%, which meant that more ore could be processed in the same amount of time. The energy consumption was reduced by 10%, leading to significant cost savings in terms of electricity bills. The recovery rates for both lead and zinc concentrates also improved, enhancing the overall profitability of the mine. Moreover, the durability of the ceramic balls led to a reduction in maintenance costs, as the frequency of replacement was much lower compared to steel balls.
Case Study 2: Purity Enhancement in a European Mine
In Europe, a lead-zinc mine was facing challenges related to metallic contamination from steel grinding media. This was affecting the quality of the lead and zinc concentrates and their compliance with export quality standards. By switching to ceramic grinding balls, the mine was able to achieve higher purity in the concentrates. The absence of metallic impurities ensured better quality and made the concentrates more marketable. The uniform particle size achieved by the ceramic balls also enhanced the flotation efficiency, further improving the overall performance of the mining operation.
Case Study 3: Environmental Benefits in a South American Mine
A South American lead-zinc mine embraced ceramic grinding balls as part of its sustainability initiative. The benefits were far-reaching. The waste generation was reduced due to the long lifespan of the ceramic balls. The lower energy usage contributed to a more environmentally friendly operation. Additionally, the improved tailings management made the mine more compliant with environmental regulations and reduced its impact on the surrounding ecosystem.
Optimizing Ceramic Grinding Balls for Lead-Zinc Mining
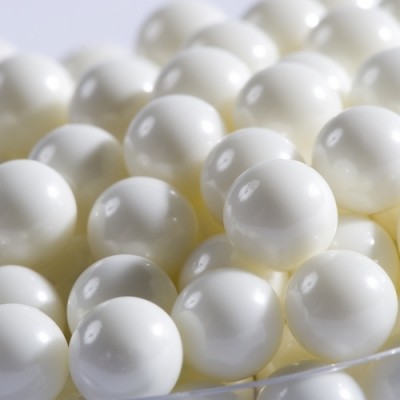
Material Composition
The choice of material composition for ceramic grinding balls is a crucial factor. Zirconia beads are highly recommended for ultra-fine grinding applications. Their high density and strength make them ideal for achieving the finest particle sizes. Alumina balls, on the other hand, offer a cost-effective solution for medium-fine grinding. They provide a good balance between performance and cost, making them suitable for a wide range of lead-zinc mining operations.
Size and Density
Selecting the correct size and density of ceramic grinding balls is essential for efficient grinding and energy consumption optimization. For lead-zinc ore, a combination of medium and fine-sized ceramic balls is often the best approach. The medium-sized balls can handle the initial grinding, while the fine-sized balls can further refine the particle size. The density of the balls should be chosen based on the specific characteristics of the ore and the grinding equipment to ensure maximum energy transfer and efficient grinding.
Operational Parameters
Optimizing mill speed, slurry density, and grinding time is vital for enhancing the performance of ceramic grinding balls. The mill speed should be adjusted to ensure that the balls have the right impact force on the ore. The slurry density affects the fluid dynamics inside the mill and should be optimized for efficient grinding. The grinding time needs to be carefully controlled to achieve the desired particle size without over-grinding. Regular monitoring and adjustments of these operational parameters are necessary to ensure consistent and optimal results.
Supplier Quality
Partnering with a reputable supplier is of utmost importance. Sanxin New Materials Co., Ltd. is an example of a reliable supplier that offers a range of ceramic grinding balls designed specifically for mining applications. A good supplier will ensure that the ceramic balls meet the required quality standards, have consistent properties, and are tailored to the specific needs of the lead-zinc mine.
Future Trends in Ceramic Grinding Media for Lead-Zinc Mines
1. Nanotechnology Integration
The integration of nanotechnology into ceramic grinding balls is an exciting prospect. Nanoparticles can be incorporated into the ceramic matrix to enhance its properties. This could lead to ceramic balls with even higher hardness, improved wear resistance, and superior chemical stability. The enhanced properties would further improve the grinding performance and durability of the balls, making them even more suitable for the demanding conditions of lead-zinc mining.
2. Sustainability Focus
With the growing global emphasis on sustainable mining practices, ceramic grinding balls will continue to play a central role. Their durability, energy efficiency, and low environmental impact make them an ideal choice for eco-friendly mining operations. Future research and development efforts will likely focus on further improving these aspects and exploring new ways to make ceramic grinding balls even more sustainable.
3. Automation and AI Optimization
The integration of automation and artificial intelligence in mining processes will revolutionize the use of ceramic grinding media. Real-time monitoring and optimization of the performance of ceramic balls will be possible. AI algorithms can analyze data from sensors placed in the grinding equipment and adjust the operational parameters such as mill speed, slurry density, and grinding time to ensure maximum efficiency. This will lead to further reductions in operational costs and improvements in overall productivity.
Conclusion
Ceramic grinding balls have truly transformed the lead-zinc mining industry. Their applications in crushing, grinding, flotation, and tailings management, along with their numerous benefits such as enhanced wear resistance, minimal contamination, energy efficiency, and environmental advantages, make them an indispensable asset. The case studies from various mines around the world clearly demonstrate their value in improving efficiency, purity, and sustainability. As the industry looks towards the future, the trends of nanotechnology integration, sustainability focus, and automation and AI optimization will further enhance the capabilities of ceramic grinding balls. For high-quality ceramic grinding balls and expert guidance, contacting Sanxin New Materials Co., Ltd. via WhatsApp at +86 19070858212 or email sales@beadszirconia.com is a wise step for any lead-zinc mine looking to elevate its operations with advanced ceramic solutions tailored to its specific needs.