ZTA Wear-Resistant Ceramic Lining Bricks, the Guardian in Heavy Wear Conditions
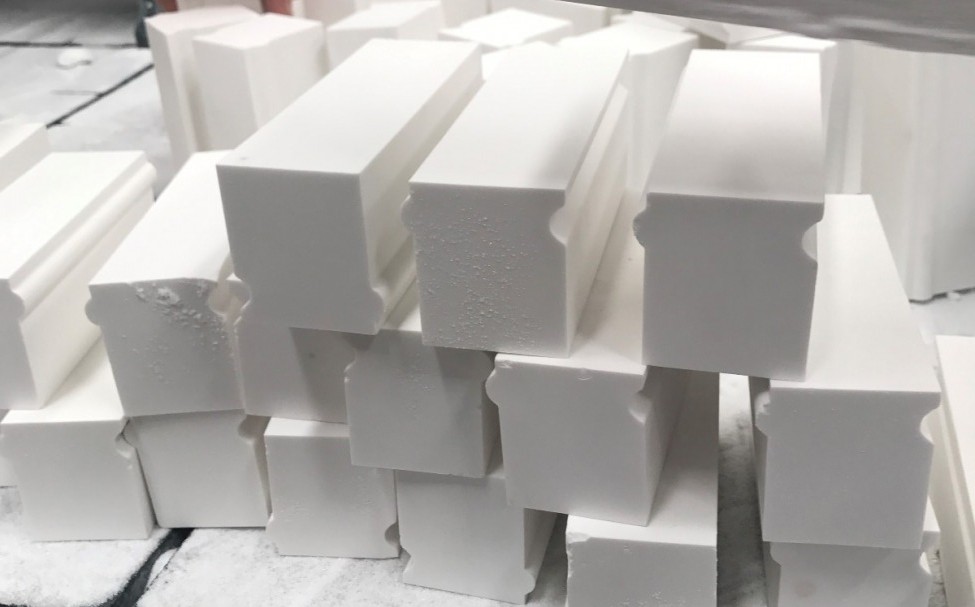
In the vast landscape of modern industrial production, the issue of equipment wear has emerged as a formidable and persistent adversary. It is a challenge that looms large, casting a shadow over the pursuit of enhanced production efficiency and cost-effective operations. Equipment wear can lead to a cascade of negative consequences, including unplanned downtime, increased maintenance expenditures, and a reduction in the overall quality and quantity of output. However, in the face of this seemingly intractable problem, the remarkable force of technological innovation has once again demonstrated its ability to surmount obstacles and pioneer novel solutions. Among these groundbreaking advancements, wear-resistant ceramic lining bricks have emerged as a true "game-changer," revolutionizing the way industries approach and address the issue of equipment wear.
Wear-resistant ceramic lining bricks, as their name so aptly suggests, possess a core strength that lies in their extraordinary wear resistance. This unique property sets them apart from traditional metal materials that have long been the mainstay in industrial applications. Ceramic materials, by virtue of their high hardness and low friction coefficient, offer a distinct advantage in minimizing the wear rate of equipment during operation. The high hardness endows them with the ability to withstand the abrasive forces exerted by various substances, be it the rough edges of ores in mining operations or the abrasive particles in industrial slurries. The low friction coefficient further reduces the frictional forces that contribute to wear and tear, allowing equipment to operate more smoothly and with less resistance.
The implications of this enhanced wear resistance are far-reaching and profound. Firstly, it translates into a significantly extended service life for equipment. In industries where heavy wear is the norm, such as mining, metallurgical processing, and building materials manufacturing, this means that equipment can remain operational for longer periods without the need for frequent replacements. For example, in a mining operation, crushers and screens that are lined with wear-resistant ceramic bricks can endure the continuous onslaught of hard and abrasive ores for an extended duration. This not only reduces the frequency of equipment breakdowns but also minimizes the associated costs of replacement parts and the downtime required for installation.
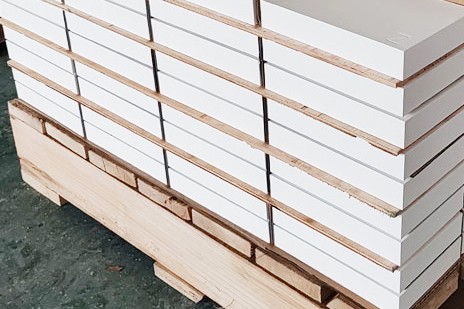
Secondly, the reduced wear rate leads to a lower maintenance frequency. Maintenance activities, which often involve significant time, labor, and financial resources, can be a major drain on industrial operations. With wear-resistant ceramic lining bricks, the need for regular maintenance, such as replacing worn-out parts or performing extensive repairs, is substantially diminished. This allows industrial facilities to allocate their resources more efficiently, focusing on core production activities rather than being constantly tied up with equipment upkeep. In a metallurgical plant, for instance, the furnaces that are protected by ceramic lining bricks require less frequent inspections and repairs, enabling the plant to maintain a more stable and continuous production process.
Finally, a more stable production process is another crucial benefit. Unplanned stoppages due to equipment wear can disrupt the entire production chain, leading to inefficiencies, missed deadlines, and customer dissatisfaction. By reducing wear and the associated risks of breakdowns, wear-resistant ceramic lining bricks contribute to a more reliable and consistent production flow. In the building materials industry, where the continuous operation of equipment such as crushers, conveyors, and mills is essential, the use of these ceramic bricks helps to ensure that production targets are met without interruption, thereby enhancing overall productivity and profitability.
The application of wear-resistant ceramic lining bricks is not confined to a single industry or a specific set of applications. Their remarkable flexibility and adaptability have enabled them to find a home in a diverse range of industrial scenarios. In the realm of mining machinery, they play a crucial role in safeguarding the integrity of crushing and screening equipment. The harsh environment of a mine, with its large volumes of abrasive ores and constant vibrations, places a heavy toll on equipment. Wear-resistant ceramic lining bricks are able to absorb the impact of the ores, protecting the underlying metal structures from premature wear and damage. They are installed in areas such as the linings of crushers, where the jaws or cones come into direct contact with the ores, as well as on the screens that separate different sizes of materials.
In the metallurgical industry, the proximity of high-temperature furnaces demands materials with not only wear resistance but also outstanding high-temperature resistance and corrosion resistance. Wear-resistant ceramic lining bricks rise to this challenge admirably. They can withstand the extreme temperatures and corrosive gases and fluxes present in metallurgical processes. For example, in a steelmaking furnace, the ceramic lining bricks protect the furnace walls from the erosive action of molten metal and slag. Their ability to maintain their structural integrity and performance under such harsh conditions is vital for ensuring the safety and efficiency of the metallurgical production process. Without the protection of these ceramic bricks, the furnace walls would quickly deteriorate, leading to leaks, energy losses, and potential safety hazards.
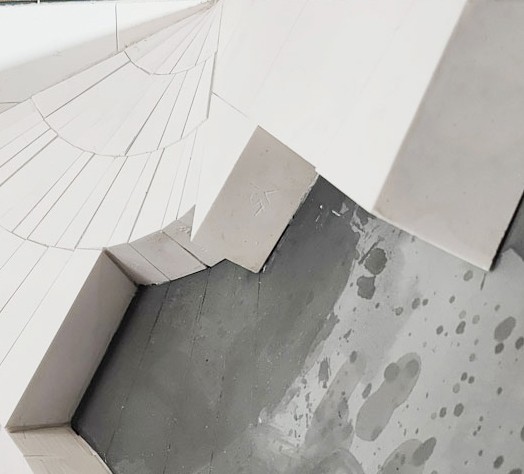
Even in the building materials industry, wear-resistant ceramic lining bricks have made a significant impact. Cement plants, for instance, are characterized by the continuous movement of abrasive materials such as limestone, clay, and cement clinker. The conveyor belts and associated equipment in these plants are constantly exposed to the abrasive action of these materials. By using wear-resistant ceramic lining bricks to reduce the direct contact between the conveyor belts and the materials, the service life of the equipment is greatly extended. This not only reduces the frequency of belt replacements but also minimizes the spillage and loss of materials during transportation, leading to improved operational efficiency and cost savings.
In addition to their wear resistance and adaptability, wear-resistant ceramic lining bricks also offer other advantages. They have excellent chemical stability, which means they are resistant to a wide range of chemical substances that may be present in industrial processes. This chemical inertness ensures that the bricks do not react with the materials being processed or the surrounding environment, thereby maintaining their performance and integrity over time. Moreover, ceramic materials are generally lightweight compared to metal alternatives, which can be beneficial in terms of reducing the overall weight of equipment and facilitating installation and transportation.
The manufacturing process of ZTA wear-resistant ceramic lining bricks is a complex and highly technical one. It typically involves the careful selection and preparation of raw materials, including high-purity alumina and zirconia powders. These powders are then mixed in precise proportions to achieve the desired properties of the final product. The mixture is then formed into the shape of bricks using various forming techniques, such as pressing or casting. After forming, the bricks undergo a series of heat treatment processes, including sintering, which is crucial for densifying the ceramic material and enhancing its mechanical properties. The sintering temperature and time are carefully controlled to ensure that the bricks achieve the optimal combination of hardness, strength, and wear resistance.
Quality control is a vital aspect of the production of wear-resistant ceramic lining bricks. Stringent testing procedures are implemented at various stages of the manufacturing process to ensure that the bricks meet the required standards. These tests include measurements of hardness, density, porosity, and wear resistance. Non-destructive testing methods such as ultrasonic inspection may also be used to detect any internal defects or cracks in the bricks. Only those bricks that pass the rigorous quality control checks are deemed suitable for use in industrial applications.
The installation of wear-resistant ceramic lining bricks also requires careful consideration and expertise. Proper installation is essential to ensure that the bricks perform effectively and provide the desired level of protection. The surface on which the bricks are to be installed must be clean, dry, and properly prepared. Adhesives or mortar systems are used to bond the bricks to the substrate, and the installation process must be carried out in accordance with the manufacturer's instructions. In some cases, additional measures such as anchoring or mechanical fixation may be required, especially in applications where the bricks are subject to high levels of impact or vibration.
The future of wear-resistant ceramic lining bricks looks promising. As industries continue to demand higher levels of performance and durability from their equipment, the development and innovation of ceramic materials are likely to accelerate. Researchers are constantly exploring new formulations and manufacturing techniques to further enhance the properties of wear-resistant ceramics. For example, the addition of nanoparticles or the use of advanced sintering technologies may lead to ceramics with even greater hardness, toughness, and wear resistance. Additionally, the application of wear-resistant ceramic lining bricks may expand into new industries and fields, such as renewable energy, where the need for reliable and long-lasting equipment is also crucial.
In conclusion, ZTA wear-resistant ceramic lining bricks have emerged as a powerful solution in the battle against equipment wear in heavy wear conditions. Their exceptional wear resistance, combined with their flexibility, adaptability, and other advantageous properties, has made them an indispensable asset across a wide range of industries. From mining to metallurgy to building materials and beyond, these ceramic bricks are playing a vital role in enhancing production efficiency, reducing maintenance costs, and ensuring the reliable and safe operation of industrial equipment. As technology continues to advance, we can expect to see even more remarkable developments in the field of wear-resistant ceramics, further solidifying their position as the guardians of industrial equipment in the face of the ever-present challenge of wear and tear.