In the complex and demanding industrial landscape, the need for reliable and efficient hot air duct systems has led to continuous exploration and innovation. Wear - resistant ceramic hot air ducts have emerged as a remarkable solution, finding extensive applications in diverse industries. Their growing popularity in sectors like power plants and steel manufacturing is a testament to their unique capabilities. This comprehensive article will explore in great detail the key characteristics that make these ducts so special and provide in - depth guidelines for their installation to ensure they perform optimally and have a long lifespan.
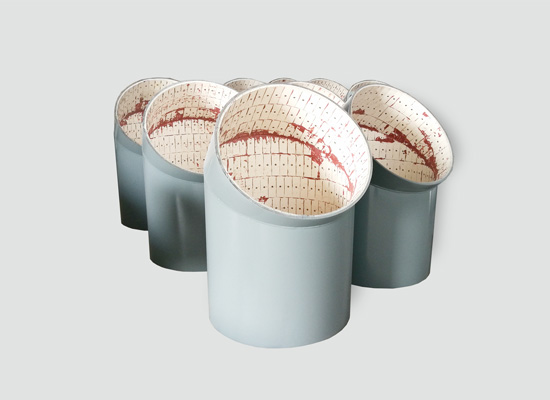
At the very core of wear - resistant ceramic hot air ducts is alumina ceramic, a material with extraordinary properties. One of the most significant features of alumina ceramic is its remarkable hardness, which exceeds HRA88 on the hardness scale. This level of hardness is not easily achieved by other common materials used in duct construction. It is the result of the unique atomic structure and bonding within the alumina ceramic. The strong ionic and covalent bonds between the aluminum and oxygen atoms give the material its hardness, making it highly resistant to deformation and penetration.
This high hardness endows the ceramic hot air ducts with outstanding wear resistance. In industrial settings, these ducts are often subjected to extremely harsh operational environments. For example, in power plants, hot air ducts may be exposed to high - velocity airflows carrying fine particles of ash and other debris. In steel manufacturing, the ducts can encounter abrasive materials such as metal dust and scale. The hardness of the alumina ceramic enables the ducts to withstand these abrasive forces without significant wear. The ceramic surface remains intact, preventing the formation of scratches, gouges, or other forms of damage that could compromise the structural integrity of the ducts. This wear resistance is crucial as it ensures that the ducts can maintain their functionality over extended periods, even under the most demanding conditions.
The robust nature of alumina ceramic goes beyond just wear resistance. It also ensures the long - term structural integrity of the hot air ducts. Unlike some materials that may degrade over time due to chemical reactions, mechanical stress, or thermal cycling, alumina ceramic remains stable. The ceramic's internal structure is highly resistant to cracking and fracture, even when subjected to continuous mechanical vibrations or thermal expansion and contraction. This stability means that the ducts can maintain their shape and performance characteristics, providing reliable service for years without the need for frequent repairs or replacements.
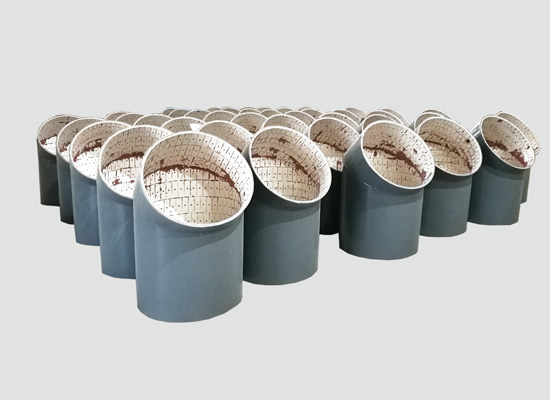
One of the standout features of wear - resistant ceramic hot air ducts is their ability to operate efficiently in high - temperature settings. This remarkable capability is largely due to the chemical stability of alpha - alumina, which is a key component of the ceramic material. Alpha - alumina has a stable crystal structure that is highly resistant to chemical reactions, even at elevated temperatures. This stability is a result of the strong ionic bonds within the crystal lattice. The aluminum and oxygen atoms are tightly held together, preventing the rearrangement of atoms or the breakdown of the structure under the influence of heat.
The chemical stability of alpha - alumina provides these ducts with excellent resistance to thermal degradation. In high - temperature environments, many materials start to undergo significant changes. Metals may oxidize, plastics may melt or decompose, and other ceramics may experience phase transitions or structural breakdown. However, the alpha - alumina in these ceramic ducts remains unaffected. This allows the ducts to function seamlessly in environments where temperatures can soar to extreme levels. For instance, in certain power generation processes, hot air temperatures can reach several hundred degrees Celsius. The ceramic hot air ducts can handle these temperatures without any risk of material failure or damage due to excessive heat. This high - temperature tolerance makes them ideal for applications in industries where thermal conditions are a critical factor, ensuring the continuous and reliable operation of the industrial processes that rely on the hot air ducts.
For applications where the duct operating temperature does not exceed 350°C, high - temperature ceramic adhesives are the recommended choice for bonding the ceramic components. The process of using these adhesives is relatively straightforward. First, the surfaces of the ceramic pieces to be joined are carefully cleaned to remove any dirt, grease, or other contaminants that could interfere with the bonding process. Then, the adhesive is applied evenly to one or both of the mating surfaces. The ceramic components are then carefully aligned and pressed together, allowing the adhesive to spread and fill any gaps between the surfaces.
This method is favored for several reasons. One of the main advantages is its simplicity. It does not require specialized technical expertise or complex equipment. Installation teams with basic training can easily handle the adhesive bonding process. Additionally, it is a cost - effective solution. The cost of the adhesive and the associated application tools is relatively low compared to other installation methods. The adhesive provides a reliable bond, ensuring that the ducts remain securely in place during normal operation. It fills the microscopic gaps between the ceramic surfaces, creating a continuous connection that can withstand the mechanical forces exerted during operation.
However, it is important to note that this method has certain limitations. The bond strength of the adhesive is temperature - dependent. As the operational temperature approaches or exceeds the adhesive's threshold, the adhesive may start to lose its cohesive strength. This can lead to the detachment of ceramic components. In some cases, the adhesive may soften or even decompose at higher temperatures, causing the bond to fail. Therefore, careful consideration of the maximum operating temperature is essential when choosing adhesive bonding as the installation method. If the temperature in the duct system is expected to fluctuate near the adhesive's limit, alternative installation techniques may need to be considered to ensure the long - term stability of the ducts.
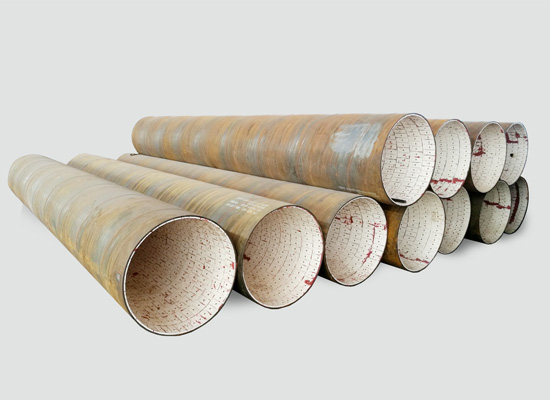
In scenarios where the operational temperature surpasses 350°C, bolted welding becomes the preferred installation method. This technique involves a combination of using threaded bolts and welding to secure the ceramic ducts firmly. First, the ceramic ducts are carefully aligned, and holes are drilled at appropriate positions for the bolts. The threaded bolts are then inserted through the holes, and nuts are tightened to hold the ducts in place initially. After the bolts are in position, welding is performed at the joints. The welding process requires skilled professionals who are trained in high - temperature welding techniques. Special welding electrodes and equipment are used to ensure that the welds are of high quality and can withstand the high - temperature environment.
Bolted welding offers several significant advantages. It provides a more robust and durable connection compared to adhesive bonding. The combination of bolts and welding distributes the mechanical stresses more effectively, especially in high - temperature and high - stress environments. The bolts act as a primary means of holding the ducts together, while the welding further reinforces the connection. This dual - connection method can withstand higher temperatures and greater mechanical stresses without compromising the integrity of the ductwork. Even if there are small cracks or failures in the welds due to thermal cycling or other factors, the bolts can still maintain the structural integrity of the ducts, minimizing the risk of a catastrophic failure.
Although this method is more complex and requires skilled professionals, the enhanced stability and reliability it provides make it indispensable for high - temperature applications. The welding process demands a high level of precision and expertise. The welders need to have a good understanding of the properties of the ceramic material and the behavior of the weld pool at high temperatures. They must also be able to control the welding parameters such as current, voltage, and welding speed to ensure that the welds are free from defects such as porosity, cracks, or incomplete fusion. Additionally, the special equipment used for high - temperature welding, including the welding power source and the electrodes, needs to be of high quality and properly maintained to ensure reliable operation.
In addition to mechanical stability, the sealing integrity of ceramic hot air ducts is of utmost importance, especially when transporting specialized materials. In many industrial processes, the materials being transported through the ducts are often valuable, hazardous, or both. For example, in chemical processing, the hot air may carry corrosive gases, volatile organic compounds, or fine particles of reactive chemicals. In such cases, any leakage from the duct system can have severe consequences. It can lead to environmental pollution, endanger the health and safety of workers, and cause significant losses of valuable materials. Therefore, ensuring a leak - proof operation of the ceramic hot air ducts is crucial for the overall efficiency and safety of the industrial process.
To address the issue of sealing, seamless or monolithic ceramic pipes are highly recommended for applications requiring stringent sealing. These one - piece ceramic ducts are manufactured using advanced ceramic forming techniques that eliminate the presence of joints. Joints in traditional duct systems are often the weakest points, as they can be prone to leaks due to gaps, poor bonding, or mechanical stress. By eliminating joints, seamless ceramic pipes provide a continuous and homogeneous structure that ensures a high - level of sealing integrity. Even under extreme conditions, such as high pressures or temperature variations, these one - piece ducts can maintain their leak - proof performance. This not only protects the environment and the safety of the workplace but also ensures the efficient operation of the industrial process by preventing the loss of materials being transported through the ducts.
The high hardness and thermal stability of alumina ceramic are the key factors contributing to the extended service life of these hot air ducts. The wear - resistant properties of the ceramic prevent the ducts from deteriorating due to abrasion caused by the flow of hot air containing particles. Over time, traditional duct materials may wear thin, leading to leaks or failures. However, the alumina ceramic ducts can maintain their thickness and integrity, even after years of operation. Additionally, the high - temperature stability ensures that the ducts can withstand the thermal stresses associated with repeated heating and cooling cycles. This combination of wear and thermal resistance results in ducts that can operate for extended periods without significant degradation, reducing the need for frequent replacements. In industries where downtime for duct replacement can be extremely costly, this extended service life translates to significant savings in terms of both time and money.
The superior wear and high - temperature resistance of the ceramic hot air ducts directly translate to enhanced performance in demanding environments. The ducts can maintain a consistent cross - sectional area and a smooth inner surface, which is crucial for efficient hot air flow. A smooth inner surface reduces the friction between the hot air and the duct walls, minimizing pressure losses and ensuring a more uniform flow of air. This consistent performance ensures that the industrial processes relying on the hot air ducts, such as heating, drying, or chemical reactions, can be carried out with high efficiency and reliability. There is no loss of pressure or flow rate due to duct degradation, resulting in better overall process control and improved product quality. For example, in a drying process in the food or pharmaceutical industry, consistent hot air flow provided by ceramic ducts can ensure even drying of the products, reducing the risk of spoilage or inconsistent quality.
Although the initial investment in wear - resistant ceramic hot air ducts may be higher compared to traditional duct materials, the long - term cost benefits are substantial. The reduced need for maintenance, repairs, and replacements over the life of the ducts leads to lower overall costs. Traditional ducts may require frequent inspections, patching, or complete replacement due to wear, corrosion, or thermal damage. In contrast, ceramic ducts with their durable nature require minimal maintenance. Additionally, the improved energy efficiency resulting from the stable performance of the ceramic ducts can further contribute to cost savings. For example, in power plants, efficient hot air ducts can reduce heat losses during the transfer of hot air from the combustion chamber to other parts of the system. This reduction in heat loss means that less fuel is needed to maintain the required temperature, resulting in lower operating costs.
The robust construction of the ceramic hot air ducts minimizes the risk of leaks and failures. The combination of high - quality alumina ceramic, proper installation techniques, and seamless sealing options ensures that the ducts can operate safely even in hazardous environments. In industries such as chemical processing and power generation, where safety is a top priority, the reliability of the hot air duct system is crucial. Leaks in the duct system can lead to the release of hot gases, chemicals, or even cause fires or explosions. By reducing the potential for leaks and other failures, these ceramic ducts contribute to a safer working environment. Workers can carry out their tasks without the fear of sudden duct failures, and the overall operation of the industrial plant can proceed without disruptions caused by duct - related issues.
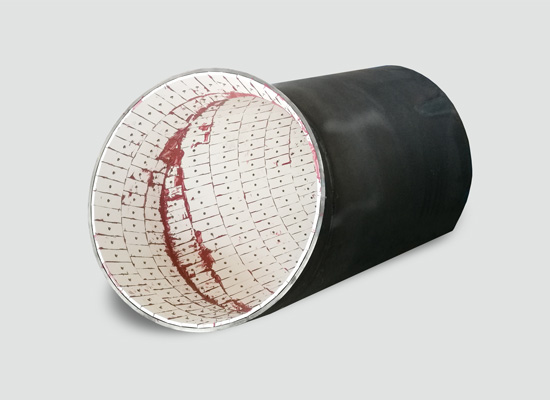
In power plants, wear - resistant ceramic hot air ducts play a vital role in ensuring efficient and reliable airflow. Whether it's in coal - fired, gas - fired, or nuclear power plants, the hot air ducts are used in various systems such as combustion air supply, flue gas exhaust, and heat recovery systems. In coal - fired power plants, the hot air ducts are exposed to high - temperature flue gases containing ash and other particulate matter. The wear - resistant ceramic ducts can withstand the abrasive action of these particles and the high temperatures without significant degradation. In gas - fired power plants, the ceramic ducts can handle the hot combustion gases efficiently, ensuring that the heat is properly transferred to the steam generation system. In nuclear power plants, where safety and reliability are of utmost importance, the ceramic hot air ducts provide a stable and durable solution for transporting hot air in ventilation and cooling systems.
The steel manufacturing process involves intense heat and the presence of abrasive materials. Hot air ducts are used in heating and ventilation systems within steel plants to provide the necessary heat for various processes such as melting, refining, and drying. During the melting process, the hot air ducts are subjected to extremely high temperatures and may be exposed to molten metal splashes or dust from the raw materials. The wear - resistant ceramic hot air ducts can endure these harsh conditions without failing. The ceramic material's ability to withstand high - temperature and abrasion ensures that the hot air supply remains stable and efficient, contributing to the quality and productivity of the steel manufacturing process. For example, in a continuous casting operation, consistent hot air flow provided by ceramic ducts can help in drying the molds and improving the quality of the cast steel.
Chemical processing plants often deal with corrosive and high - temperature chemical environments. The hot air ducts in these plants are used to transport hot gases or vapors that may contain corrosive chemicals. Wear - resistant ceramic hot air ducts are ideal for such applications as they are chemically inert and can withstand the high - temperature and corrosive conditions. In chemical reactions that require precise temperature control, the ceramic ducts can maintain a stable hot air supply without being affected by the chemicals in the environment. The seamless or well - sealed ceramic ducts prevent the leakage of hazardous chemicals, protecting the environment and the safety of the plant workers. For instance, in a chemical plant producing fertilizers, the ceramic hot air ducts can transport hot gases containing ammonia or other reactive chemicals without any risk of leakage or chemical reaction with the duct material.
In automotive manufacturing plants, the durability of heating and ventilation systems is crucial. Wear - resistant ceramic hot air ducts can enhance the performance of these systems by providing reliable heat transfer. In the painting and drying processes of automotive parts, the hot air ducts are used to supply hot air for curing the paint. The high - temperature resistance of the ceramic ducts ensures that they can handle the heat generated during these processes. Additionally, the wear resistance of the ceramic material reduces the need for maintenance and replacements, improving the overall efficiency of the automotive manufacturing process. The ceramic ducts can also be used in the ventilation systems of the manufacturing plant to maintain a comfortable working environment for the workers.
Wear - resistant ceramic hot air ducts represent a pivotal advancement in industrial ducting solutions, offering unmatched durability and high - temperature resilience. Understanding their unique features, such as the exceptional hardness of alumina ceramic, high - temperature performance, and the importance of proper installation, is key to maximizing their benefits. By following the recommended installation practices, whether using high - temperature ceramic adhesives for lower - temperature applications or bolted welding for higher - temperature scenarios, industries can ensure the long - term reliability and efficiency of these ducts. The seamless sealing options further enhance their performance, especially in applications involving specialized material transport.
For more information, contact Sanxin New Materials Co., Ltd. via WhatsApp at +86 19070858212 or email sales@beadszirconia.com.