In the realm of industrial infrastructure, pipelines are the arteries that facilitate the flow of various substances, be it in mining, power generation, chemical processing, or the oil and gas sector. However, when faced with the "Three High" conditions of high temperature, high velocity, and severe wear caused by hard particles, traditional pipeline materials often prove inadequate. This has spurred the development and application of advanced ceramic technology, which has emerged as a revolutionary solution to enhance pipeline durability and performance.
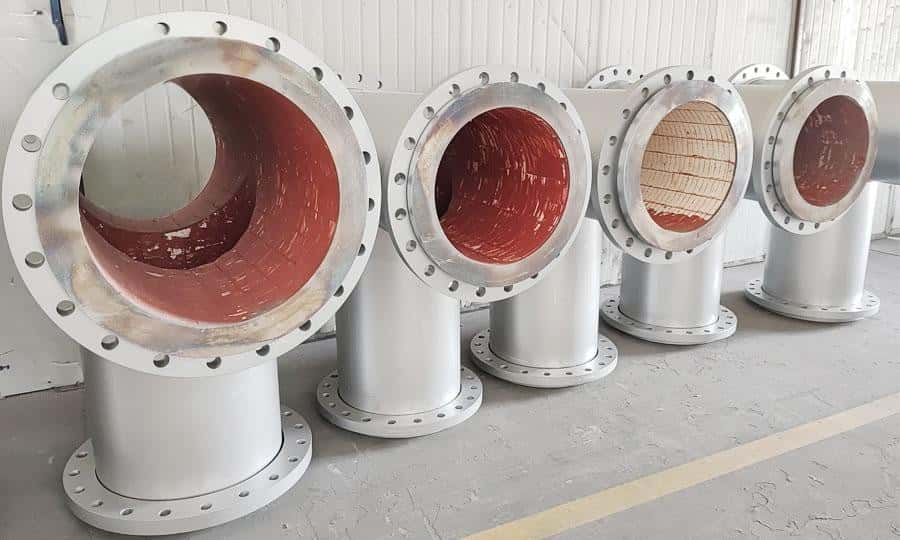
Pipelines operating under "Three High" conditions are subjected to an extremely harsh environment. High temperatures can cause materials to soften, lose their strength, and even undergo phase changes, leading to structural degradation. Abrasive particles, such as those found in mining slurries or industrial waste streams, can erode the inner surface of the pipeline at a rapid pace. Simultaneously, high-velocity flows increase the kinetic energy of the abrasive particles and the fluid itself, exacerbating the wear and tear. For instance, in a coal-fired power plant, the steam flowing through the pipelines at high speeds and temperatures can carry particulate matter that continuously bombards the pipe walls.
For manufacturers of wear-resistant ceramic elbows and tees, these challenges present a double-edged sword. On one hand, the demand for solutions to combat the "Three High" conditions offers a significant market opportunity. Industries are willing to invest in durable pipeline systems to avoid costly downtime, frequent maintenance, and replacement of equipment. On the other hand, the technical difficulties associated with developing and manufacturing such advanced ceramic-lined pipelines are substantial. The innovation required to create materials that can withstand these extreme conditions demands extensive research and development. Moreover, the installation techniques for ceramic-lined pipelines are complex and require specialized skills and equipment. For example, ensuring proper alignment and bonding of the ceramic lining within the steel pipe is crucial, and any misstep can lead to premature failure.
Ceramic-lined components, such as elbows and tees, are engineered to endure temperatures well above 500°C. The steel components that form the outer structure of these pipelines are subject to meticulous quality control procedures. X-ray inspection of welds is a standard practice to detect any internal flaws or discontinuities that could compromise the integrity of the pipeline under high-pressure conditions. Additionally, comprehensive pressure testing is carried out on the entire pipeline system to validate its reliability. This ensures that the pipeline can withstand the internal pressure exerted by the flowing medium, whether it is steam, a corrosive chemical, or an abrasive slurry.
The ceramic lining, which is the core of the wear-resistant properties, is fabricated through a sintering process at temperatures reaching up to 1700°C. This high-temperature treatment results in the formation of monolithic ceramic rings or seamless ceramic-lined pipes. The absence of joints or seams in these linings is a significant advantage as it eliminates potential weak points where failure could initiate. These ceramic linings are then integrated into heat-formed steel components using advanced techniques. High-temperature adhesive is applied to fill any minute gaps that may exist between the ceramic and the steel, enhancing the thermal resistance of the assembly and contributing to the overall longevity of the pipeline.
For pipelines with diameters less than 400mm, seamless ceramic-lined elbows and fittings have demonstrated remarkable performance improvements. Compared to conventional materials, they can increase the equipment lifespan by over 20 times. The seamless design and the inherent hardness and toughness of the ceramic lining make them highly resistant to wear and erosion. In applications where the flow of abrasive substances is relatively contained, such as in certain chemical processing lines or small-scale mining operations, these small-diameter ceramic-lined pipelines prove to be extremely effective.
In the case of pipelines exceeding 400mm in diameter, innovative solutions have been developed to address the unique challenges. The combination of dovetail-shaped wear-resistant alumina ceramics and stud-welding techniques is a prime example. Dovetail-shaped ceramic pieces are carefully interlocked within fixed metal strips that are welded to the interior of the pipeline. Once the adhesive cures, a seamless and highly robust lining is created. This design takes into account the thermal expansion and contraction that occurs during operation. Even under significant temperature fluctuations, the ceramics remain securely in place, ensuring the integrity of the pipeline and minimizing the risk of leaks or failures.
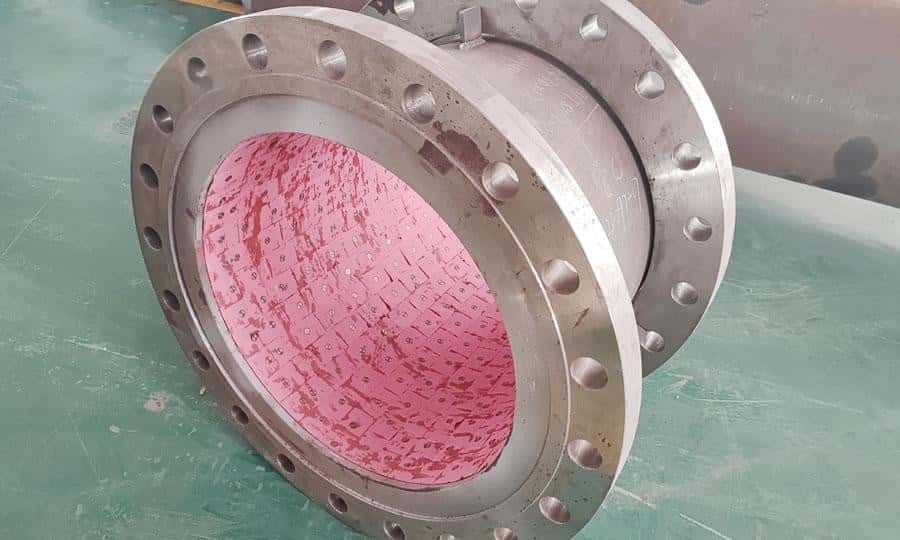
Ceramics possess a hardness that is unrivaled by most traditional pipeline materials. This hardness enables them to effectively resist erosion caused by abrasive particles in high-velocity flows. Whether it is the sharp edges of mineral particles in a mining slurry or the solid impurities in a chemical stream, the ceramic lining can withstand the continuous impact and abrasion. In contrast, materials like steel or plastic are prone to surface damage and gradual degradation under such conditions, leading to a reduction in pipeline performance and eventual failure.
By significantly reducing wear and tear, ceramic-lined pipelines can extend the operational life of equipment by up to 20 times. This has far-reaching implications for industrial operations. Reduced maintenance requirements mean fewer interruptions in production schedules, saving both time and labor costs. Minimized downtime translates into increased productivity and higher overall efficiency. Moreover, the longer lifespan of the equipment reduces the frequency of replacement, which in turn lowers the capital expenditure associated with purchasing new pipelines and related components.
One of the most notable advantages of ceramic linings is their ability to maintain structural integrity at elevated temperatures. In industries such as power generation and certain chemical processes, where high temperatures are the norm, conventional materials may experience softening, deformation, or loss of mechanical properties. Ceramic-lined pipelines, however, can continue to function reliably, ensuring the uninterrupted flow of substances and the safe operation of the industrial process. This high-temperature stability also contributes to the energy efficiency of the system, as it reduces the need for additional cooling or insulation measures.
The integration of seamless ceramic linings into the pipeline structure eliminates weak points such as joints or welds that are often the Achilles' heel of traditional pipelines. These areas are susceptible to stress concentrations, corrosion, and leakage. Advanced manufacturing and installation techniques ensure a tight, gap-free fit between the ceramic and the steel components. This enhances the overall performance of the pipeline, reducing the risk of failures and improving the safety and reliability of the industrial operation.
In the mining industry, the transportation of abrasive materials like ores and slurries is a major application area for ceramic-lined pipelines. The harsh environment, with its high levels of abrasive particles and often elevated temperatures, demands a pipeline material that can withstand the wear and tear. Ceramic-lined pipelines not only increase the lifespan of the transportation system but also improve the efficiency of ore processing by ensuring a consistent flow of materials.
Power plants, especially those using coal or other fossil fuels, deal with high-temperature and high-pressure steam. Ceramic-lined pipelines are used to transport this steam, as they can endure the extreme conditions without degradation. This helps in maintaining the efficiency of the power generation process and reducing the risk of pipeline failures that could lead to costly shutdowns and repairs.
The chemical industry handles a wide variety of corrosive and high-temperature chemical flows. Ceramic-lined pipelines are ideal for such applications as they are chemically inert and can resist the corrosive effects of acids, bases, and other reactive substances. This ensures the integrity of the pipeline and the safety of the chemical processing operations.
In the oil and gas sector, pipelines are used to transport fluids over long distances. These fluids may contain abrasive particles and be subject to high pressures and temperatures. Ceramic-lined pipelines protect against erosion and thermal damage, thereby increasing the reliability and longevity of the pipeline infrastructure and reducing the risk of leaks and environmental disasters.
The steel components of ceramic-lined pipelines require precision welding to ensure a strong and durable structure. After welding, X-ray inspections are carried out to detect any internal defects or cracks. This is followed by pressure testing, which subjects the pipeline to a pressure higher than its normal operating pressure to verify its integrity and safety. These steps are essential to ensure that the steel structure can support the ceramic lining and withstand the forces exerted by the flowing medium.
For seamless integration of the ceramic lining, different techniques are employed. In some cases, the ceramic is sintered directly into the steel components, creating a strong bond. In other instances, advanced adhesives are used to attach the ceramic pieces to the steel. These adhesives are specially formulated to withstand high temperatures and mechanical stresses, ensuring that the ceramic remains in place even under the most demanding conditions.
The dovetail design and stud-welding techniques used for large-diameter pipelines are custom solutions that address the specific challenges of these applications. The dovetail shape of the ceramic pieces allows for a secure interlocking with the metal strips, and the stud welding provides a strong mechanical connection. This combination ensures the durability and reliability of the lining, even in the presence of thermal expansion and contraction and high fluid velocities.
Nanotechnology is being explored to enhance the toughness and wear resistance of ceramics. By manipulating the microstructure of ceramics at the nanoscale, it is possible to create materials with improved mechanical properties. For example, the addition of nanoparticles can enhance the strength and fracture toughness of the ceramic, making it more resistant to cracking and chipping under stress.
The combination of ceramics with other materials is another area of active research. Hybrid materials can offer a combination of properties that neither material alone can provide. For instance, combining ceramics with polymers can result in a material that has the hardness and wear resistance of ceramics along with the flexibility and impact resistance of polymers. This could open up new applications for ceramic-lined pipelines in areas where a balance between different properties is required.
Automated manufacturing processes are being developed to increase the precision and reduce the production costs of ceramic-lined pipelines. Computer-controlled machinery can ensure more accurate shaping and placement of ceramic components, reducing human error and improving the quality of the final product. Additionally, automation can lead to higher production volumes and faster turnaround times, making ceramic-lined pipelines more accessible and cost-effective for a wider range of industries.
The use of ceramic-lined pipelines leads to significant cost savings in the long run. Reduced maintenance requirements mean lower labor and material costs for repairs and replacements. The extended equipment lifespan also reduces the need for frequent capital expenditures on new pipelines. For example, a mining company that switches to ceramic-lined pipelines may see a reduction in annual maintenance costs by tens of thousands of dollars, depending on the scale of the operation.
Improved thermal stability of ceramic-lined pipelines minimizes energy losses during high-temperature operations. In power generation and other energy-intensive industries, this can result in significant savings in fuel consumption. For instance, a thermal power plant may experience a reduction in steam losses due to the better insulation properties of the ceramic lining, leading to increased overall energy efficiency and a reduction in greenhouse gas emissions.
Durable materials like ceramics reduce waste and the need for frequent replacements. This aligns with the principles of sustainable industrial practices. By using ceramic-lined pipelines, industries can contribute to a more circular economy by reducing the consumption of raw materials and the generation of waste. Additionally, the energy savings associated with these pipelines also have a positive environmental impact.
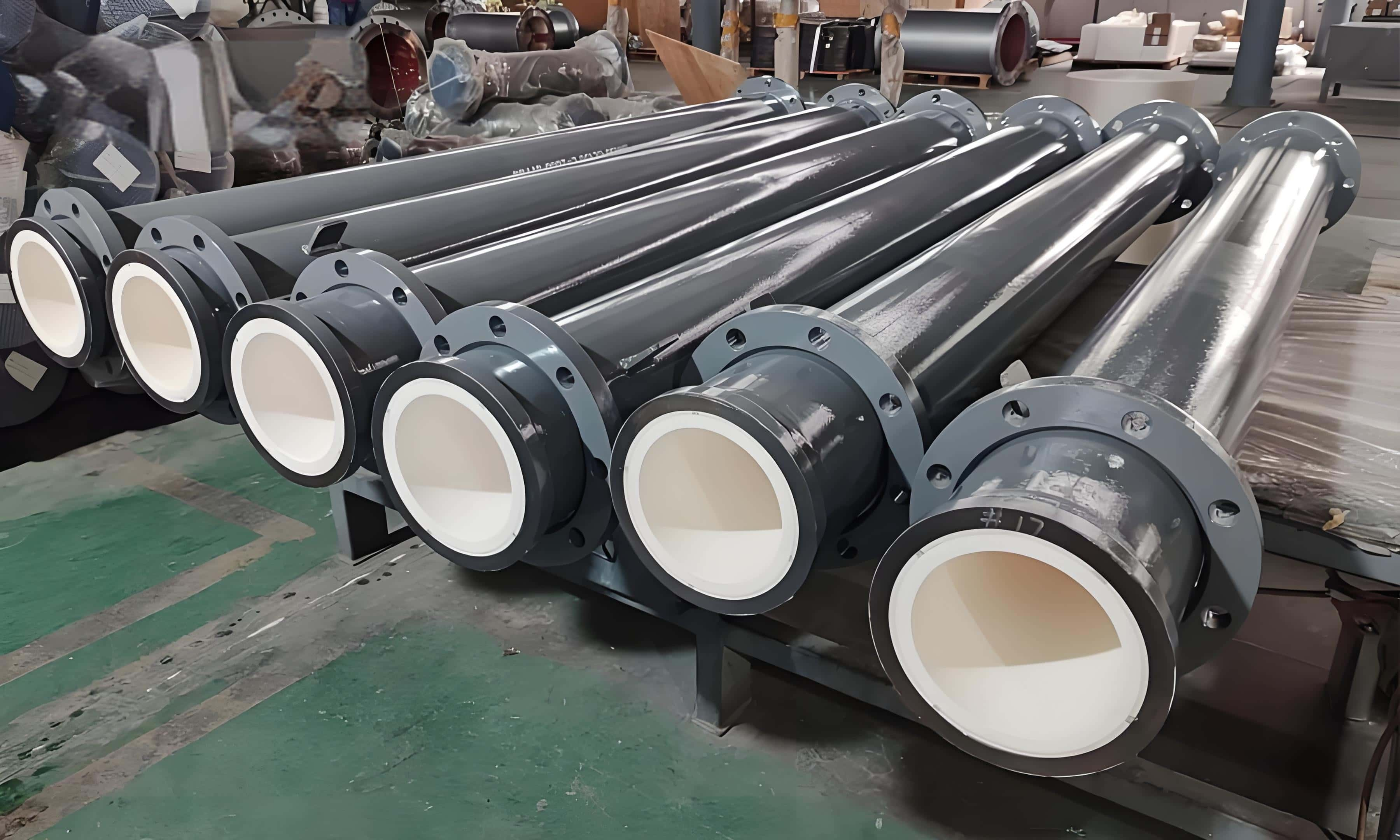
A mining operation that was dealing with abrasive iron ore slurries reported a 95% reduction in maintenance costs after switching to ceramic-lined pipelines. The previous steel pipelines were subject to frequent erosion and required regular repairs and replacements. With the ceramic-lined pipelines, the wear rate was significantly reduced, allowing the operation to run more smoothly and consistently. The increased durability also led to improved operational efficiency, as there were fewer interruptions due to pipeline failures. This enabled the plant to meet and even exceed its production targets, resulting in increased profitability.
A thermal power plant using ceramic-lined pipelines for steam transport experienced a significant decrease in downtime caused by pipeline failures. The high-temperature stability of the ceramics ensured uninterrupted operation, even during peak load conditions. Before the installation of ceramic-lined pipelines, the plant had to shut down periodically for pipeline maintenance and repairs, which affected its power generation capacity and revenue. With the new pipelines, the plant was able to operate more reliably, reducing the cost of lost production and improving its overall performance and competitiveness.
In the chemical industry, a facility handling corrosive fluids achieved greater reliability and safety by adopting ceramic-lined pipelines. The non-reactive nature of ceramics prevented chemical degradation of the pipeline, ensuring long-term performance. The previous pipelines made of metal alloys were prone to corrosion, which led to leaks and potential safety hazards. The ceramic-lined pipelines eliminated these risks, allowing the facility to operate more confidently and comply with strict safety and environmental regulations.
The future of ceramic-lined pipelines will likely involve the integration of digital monitoring systems. Sensors can be embedded within the pipelines to provide real-time data on wear, temperature, pressure, and flow rate. This information can be used to predict maintenance needs, optimize operation parameters, and prevent potential failures. For example, if the sensor detects an increase in wear rate in a particular section of the pipeline, maintenance can be scheduled before a catastrophic failure occurs, reducing downtime and costs.
3D printing technology holds great promise for the production of custom ceramic components. It allows for the creation of complex geometries and precise designs that are difficult to achieve with traditional manufacturing methods. This could lead to the development of more efficient and effective ceramic-lined pipelines with improved performance characteristics. For instance, 3D printing could enable the production of seamless ceramic linings with optimized internal structures for better fluid flow and wear resistance.
The concept of a circular economy will play an increasingly important role in the future of ceramic-lined pipelines. Efforts will be made to recycle and repurpose used ceramic materials. This could involve developing processes to reclaim and reuse the ceramic components from retired pipelines, reducing the demand for new raw materials and minimizing waste. Additionally, the energy and resources saved through recycling can contribute to a more sustainable industrial ecosystem.
As industries continue to evolve and face more demanding operating conditions, the importance of wear-resistant ceramic pipelines cannot be overstated. These pipelines offer a comprehensive solution to the "Three High" challenges, providing exceptional durability, extended equipment lifespan, high-temperature stability, and a seamless and reliable design. Their applications span multiple industries, from mining to power generation and chemical processing, with each sector reaping the benefits of improved performance and cost savings.
Manufacturers like Jiangxi Sanxin are leading the way in driving innovation and setting new standards for durability and efficiency. By embracing advanced ceramic technology and exploring future trends such as digital monitoring, 3D printing, and circular economy practices, industries can ensure sustainable growth, reduce their environmental impact, and be better prepared to handle the operational challenges of the future. The era of ceramic-lined pipelines has dawned, and it promises to revolutionize the way we think about industrial infrastructure and pipeline durability.